PLC和DCS有哪些不同点?
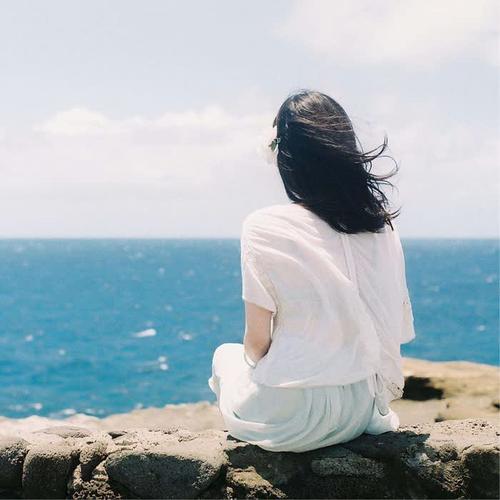
PLC和DCS有哪些不同点?
PLC(可编程逻辑控制器)和DCS(分散控制系统)是在工业自动化领域中常见的控制系统。虽然它们都用于监控和控制工业过程,但在设计和功能上有一些不同之处。
PLC(可编程逻辑控制器)
PLC是一种专门用于控制机械或工业过程的计算机系统。它具有可编程的逻辑功能,可以根据预设的程序来控制和操作各种设备。PLC通常用于较小的自动化系统,如生产线上的机器控制、机械手臂、传送带等。以下是PLC的一些特点:
灵活性和可编程性
PLC具有灵活的设计和可编程的功能,可以根据需求进行定制。它可以适应不同的工业应用,并能够处理多种输入和输出信号。
可靠性和稳定性
PLC系统经过严格测试和验证,具有高可靠性和稳定性。它们通常由可靠的硬件组成,并且可以在恶劣的工业环境中长时间运行。
快速响应和实时控制
PLC可以实时响应输入信号,并根据预设的程序进行快速控制。它们通常具有高速处理能力,可以实现精确的控制和调节。
易于维护和升级
PLC系统具有模块化的设计,易于维护和升级。如果需要更改控制逻辑或添加新功能,可以通过简单的编程来实现,而无需更换整个系统。
DCS(分散控制系统)
DCS是一种用于大型工业过程控制的系统,它由多个分布在不同位置的控制单元组成。每个控制单元负责监控和控制特定的过程或设备。以下是DCS的一些特点:
分布式架构
DCS系统采用分布式架构,其中的控制单元分散在整个工厂或设施中。这种架构使得系统更加灵活和可扩展,并且可以实现更大规模的控制。
高度集成化
DCS系统集成了多个功能,如数据采集、实时监控、报警和故障诊断等。它们通常具有强大的数据处理和分析能力,可以提供全面的过程控制和管理。
高可靠性和冗余性
DCS系统通常具有高度可靠的硬件和冗余设计,以确保在某个控制单元或组件发生故障时仍能保持系统的正常运行。这种设计使得DCS系统非常适合对工业过程进行持续监控和控制。
高级控制和优化功能
DCS系统支持高级控制和优化功能,如模型预测控制和优化算法。这些功能可以提高工业过程的效率和性能,并优化能源消耗和生产质量。
在工业自动化领域,PLC和DCS都扮演着重要的角色。选择哪种控制系统取决于具体的应用需求和工业过程的规模。PLC适用于小型和中型自动化系统,而DCS适用于大型和复杂的工业过程控制。无论是PLC还是DCS,它们都为工业生产提供了高效、可靠和安全的控制解决方案。